الصيانة الإنتاجية الشاملة (TPM)
الصيانة الإنتاجية الشاملة Total Productive Maintenance (TPM)
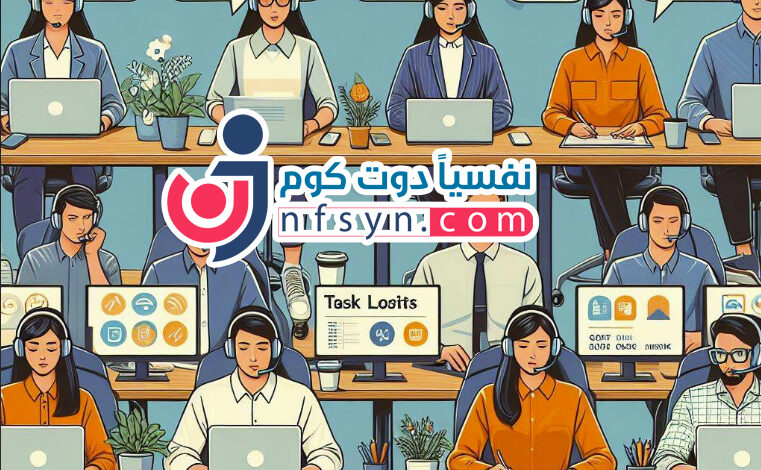
الحفاظ على معدات الإنتاج يعد ممارسة هامة للعديد من الصناعات.
أحد الطرق التي تقوم بها العديد من الشركات لصيانة معداتها هو طريقة تسمى الصيانة الإنتاجية الشاملة. معرفة ما هي وكيفية تنفيذها يمكن أن يساعدك في خلق بيئة عمل أكثر أمانًا وتحسين الإنتاجية.
في هذا المقال، سنناقش ما هي الصيانة الإنتاجية الشاملة، بما في ذلك فوائدها، وأركان الأداء وكيفية تنفيذها داخل المؤسسة.
علينا أولاً معرفة ماهي الإنتاجية :
الإنتاجية تشير إلى قدرة النظام أو الشخص أو العملية على إنتاج السلع أو الخدمات بكفاءة وفعالية، مقارنة بالموارد المستخدمة في العملية.
في سياق الصناعة، تتعلق الإنتاجية بكمية السلع المنتجة بالنسبة للموارد اللازمة لإنتاجها، مثل العمالة والمعدات والزمن. تحسين الإنتاجية يهدف إلى زيادة الإخراج باستخدام الموارد المتاحة بشكل أفضل، مما يؤدي إلى تحسين الكفاءة وتقليل التكاليف.
أنواع الإنتاجية :
توجد عدة أنواع من الإنتاجية تتنوع حسب السياق والمجالات المختلفة. من بين هذه الأنواع:
- الإنتاجية الفردية: تركز على كفاءة الأفراد في إتمام المهام وإنتاج المخرجات بشكل فعال.
- الإنتاجية العملية: ترتبط بفعالية وكفاءة العمليات والعمليات التشغيلية داخل المؤسسات والشركات.
- الإنتاجية الصناعية: تتعلق بكفاءة الإنتاج والعمليات في قطاعات الصناعة والتصنيع.
- الإنتاجية الزمنية: تركز على كيفية استخدام الوقت بشكل فعال لتحقيق أهداف الإنتاجية.
- الإنتاجية الاقتصادية: تتعلق بتحقيق أقصى قيمة من الموارد المتاحة بأقل تكلفة ممكنة.
هذه بعض الأنواع الرئيسية للإنتاجية، ويمكن أن تختلف التفاصيل والتعاريف باختلاف السياقات والمجالات.
ما هي الصيانة الإنتاجية الشاملة Total Productive Maintenance (TPM)
الصيانة الإنتاجية الشاملة هي نهج لصيانة المرافق والمعدات يركز على خلق وسيلة إنتاج مثالية. الوسيلة الإنتاجية المثالية هي مرفق ومعدات لا تتوقف، وتعمل دائمًا بأقصى كفاءة لها، ولا تحتوي على عيوب.
تعمل المؤسسات التي تتبع هذا النوع من الصيانة على خلق بيئات عمل أكثر أمانًا لموظفيها. كما أن الصيانة الإنتاجية الشاملة هي مصطلح يُستخدم أيضًا لنوع معين من المؤسسات التي تشجع أعضاء فريقها على صيانة معداتهم ومرافقهم بأنفسهم، دون تمييز بين أعضاء فريق الإنتاج وفريق الصيانة.
فوائد الصيانة الإنتاجية الشاملة Total Productive Maintenance (TPM)
هناك ثلاثة فوائد رئيسية للصيانة الإنتاجية الشاملة، وهي كما يلي:
1. إنشاء بيئة عمل أكثر أمانًا
يتدرب أعضاء الفريق على نهج الصيانة الإنتاجية الشاملة للتعرف على العيوب واستعادة ومراقبة جودة المعدات التي يعملون بها.
وهذا يعني أن كل قطعة من المعدات التي تستخدم دائمًا يتم ملاحظتها ومراقبتها، مما يؤدي إلى زيادة معدل اكتشاف العيوب المحتملة داخل أداة أو مرفق.
وهذا يؤدي أيضًا إلى زمن استجابة أسرع لإصلاح المعدات التالفة، مما يؤدي إلى إنشاء بيئة عمل أكثر أمانًا لأن المعدات دائمًا في حالة جيدة. يمكن لأعضاء الفريق الذين حصلوا على التدريب اللازم للتعرف على المخاطر تجنب المناطق الخطرة وإبلاغ الآخرين عنها للبقاء في أمان.
2. الحصول على أقل حوادث تعطّل
لنفس الأسباب التي تجعل من خلق بيئة عمل أكثر أمانًا، فإن المراقبة المستمرة للمعدات التي تستخدم بشكل مكثف يعني أن أعضاء الفريق يمكنهم في كثير من الأحيان تجنب أي مشاكل او تحديات قد تواجه المعدات وذلك بشكل استباقي.
على مستوى التنظيم، يعني ذلك تدريب أعضاء الفريق على كيفية إصلاح قطعة معينة من المعدات ومكان القطع الضرورية.
يمكن أيضًا أن يساعد ذلك المؤسسة في طلب القطع للمعدات التي تتعطّل بانتظام وضمان أن المعدات تتوقف أقل. الأمر نفسه ينطبق على المرافق – الحفاظ عليها في أفضل حالاتها الممكنة يمكن أن يؤدي إلى بيئات عمل نظيفة وفرق عمل سعداء.
3. تحقيق أداء عام أفضل
نظرًا لأن المعدات الإنتاجية تتعطل بشكل أقل وتوقفها أقل وأعضاء الفريق أكثر سعادة، يرتفع الإنتاج العام للمرفق.
يمكن أن يكون هذا مفيدًا عند النظر في تكلفة تدريب أعضاء الفريق الجدد ووضع استراتيجيات وإجراءات للتعامل مع التحديات التي قد تواجه المعدات والمرافق.
يمكن أن تزيد هذه الطريقة من الصيانة أيضًا من الأرباح لأن المؤسسة لا تحتاج إلى تخصصيين لإصلاح المعدات باستمرار. على سبيل المثال، يمكن للموظفين المدربين في المطبخ الحفاظ على سكاكينهم وأفرانهم ومواقد طهيهم دون الاعتماد على فنيين مدربين للحفاظ على المعدات في حالة جيدة، مما يوفر المال على الخدمات.
أركان الصيانة الإنتاجية الشاملة Total Productive Maintenance (TPM)
هناك ثمانية أركان للصيانة الإنتاجية الشاملة يمكن للمؤسسة تنفيذها لاستخدام هذا النوع من الصيانة:
1. الصيانة الذاتية
هذه الركن الذي يضع صيانة المعدات والآلات والمرافق عمومًا على عاتق الأشخاص الذين يستخدمونها. يمكن أن يساعد هذا الأمر أعضاء الفريق في الشعور بأن لديهم مزيدًا من السيطرة على الظروف التي يعملون فيها وأداء معداتهم.
وهناك العديد من الفوائد لهذا الركن، بما في ذلك:
- تحرير العمال الفنيين للقيام بمهام على مستوى أعلى
- منح المشغلين شعور بالملكية أكبر للمعدات التي يستخدمونها
- التعرف على التحديات الناشئة قبل أن تتحول إلى مشاكل في المعدات
- زيادة معرفة المشغلين بمعداتهم
- ضمان تنظيف وتشحيم جيد للمعدات مما يضمن اداء وكفاءة عالية تخرج من المعدات
2. الصيانة المخططة (المجدولة)
هذا هو الركن الذي يسمح للمؤسسة بإنشاء جدول منظم لصيانة المعدات والمرافق.
يمكن للمؤسسة أن تستند إلى عدة عوامل في وضع الجدول، بما في ذلك التنبؤات حول موعد فشل قطعة معينة من المعدات أو معدلات الفشل القياسية ( متوسط الفترة التي تأخذها المعدة قبل أن تحتاج إلى صيانة ) . من فوائد هذا الركن:
- تقليل حالات التوقف غير المخطط لها
- تقليل مخزون قطع الغيار المعرضة للفشل والتآكل
- جدولة الصيانة لتنفيذها أثناء إغلاق المرفق وعدم استخدام المعدات
3. الجودة
هذا هو الركن الذي يركز على تصميم إجراءات كشف الأخطاء والمعايير وأفضل الممارسات للقضاء على الأخطاء المتكررة في المعدات أو الآلات أو المرافق.
يمكن أن يتضمن ذلك تتبع التحديات إلى مصدرها من خلال تحليل السبب الجذري. من فوائد هذا الركن:
- التركيز على مشاريع التحسين لإزالة الأسباب الجذرية للمشاكل المتكررة
- الحد من تكاليف المعدات أو المرافق من خلال اكتشاف الأخطاء في وقت مبكر
- الحد من العدد الإجمالي للعيوب في المعدات أو الآلات أو المرافق
- الحد من العدد الإجمالي للعيوب في السلع التي يتم إنتاجها في المرفق
4. التحسين المركز
هذا هو الركن الذي يتيح للفرق العمل بالتعاون معًا لإنشاء خطط استباقية للحفاظ على المعدات في حالة عمل جيدة واقتراح تحسينات تدريجية لتشغيل وصيانة المعدات والمرافق.
يمكن أيضًا أن يتضمن استخدام سيناريوهات افتراضية للسماح للفرق والأفراد بإنشاء خطط استجابة للتحديات الشائعة في مكان العمل. من فوائد هذا الركن:
- دمج مواهب الفريق المجتمعة للمحترفين لتحقيق تحسين مستمر داخل المؤسسة
- حل التحديات المتكررة من خلال إنشاء فرق عمل متعددة الاختصاصات
5. إدارة المعدات المبكرة
هذا هو الركن الذي يوجه المعرفة العملية التي يكتسبها أعضاء الفريق والمؤسسة من خلال الصيانة الإنتاجية الشاملة والعمل مع معدات التصنيع إلى المعدات الجديدة.
يمكن أن يتيح ذلك للمؤسسة تحديد ما إذا كانت بحاجة إلى قطعة معدات جديدة لإنتاجها وما هي التكاليف والفوائد المرتبطة بهذه المعدات. من فوائد هذا الركن:
- الوصول إلى مستويات الأداء المخططة بسرعة أكبر مع المعدات الجديدة لأن هناك أقل عدد من التحديات الأولية
- يصبح الحفاظ على المعدات أسهل بسبب استعراض أعضاء الفريق ومشاركتهم قبل أن تركب المؤسسة المعدات الجديدة
6. التدريب والتعليم
هذا الركن يركز على أعضاء المؤسسة، بما في ذلك المشغلين والعمال الفنيين والمديرين.
يتضمن ضمان أن كل عضو في المؤسسة لديه تدريبًا متعلقًا بصيانة المعدات وأهداف الصيانة الإنتاجية الشاملة. من فوائد هذا الركن:
- تطوير مهارات الصيانة للمعدات من خلال الروتين وتحديد التحديات مع ظهورها
- تدريب المديرين على مبادئ الصيانة الإنتاجية الشاملة، وتدريب وتطوير أعضاء الفريق
- تطوير عمال الصيانة الذين يعرفون تقنيات الصيانة التنبؤية والوقائية
7. السلامة، الصحة، والبيئة
هذا الركن يركز على الحفاظ على بيئة عمل آمنة.
يتضمن أن يكون المرء على دراية بالإنتاج والمخاطر في المرفق. من فوائد هذا الركن:
- تحديد أهداف محددة لبيئة عمل خالية من الحوادث
- القضاء على المخاطر المحتملة للصحة والسلامة، وخلق بيئة عمل أكثر أماناً
8. الصيانة الإنتاجية الشاملة في الإدارة
هذا الركن يطبق أهداف وتقنيات الصيانة الإنتاجية الشاملة على الوظائف الإدارية.
يتضمن تطبيق المبادئ على جميع مستويات المؤسسة لخلق أهداف ومشاريع ونمو موحدة. من فوائد هذا الركن:
- دعم أهداف الإنتاج من خلال تحسين العمليات مثل التوريد والجدولة ومعالجة الطلبات
- توسيع فوائد إدارة الإنتاج الشاملة إلى المهام الإدارية لتقليل الفاقد على كل مستوى في المؤسسة
كيفية تنفيذ الصيانة الإنتاجية الشاملة Total Productive Maintenance (TPM)
فيما يلي خمس خطوات يمكنك استخدامها لتنفيذ نهج الصيانة الإنتاجية الشاملة:
1. تحديد منطقة البداية للتحسين
الخطوة الأولى في عملية التنفيذ هي العثور على منطقة للتحسين. هناك بعض الطرق التي يمكنك استخدامها للتعامل مع هذه الخطوة:
- الأسهل للتحسين: هذا الخيار جيد للمؤسسات التي ليست لديها خبرة في الصيانة الإنتاجية الشاملة ويمكن أن يوفر طريقة سريعة لإظهار فوائد العملية.
- ذات القيود: على الرغم من أن هذا الخيار يحمل مخاطر أعلى، إلا أنه يمكن أن يوفر زيادة فورية في الإنتاج، مما يمكن أن يظهر للإدارة العليا فوائد الصيانة الإنتاجية الشاملة.
- الأكثر مشاكل : هذا الخيار جيد لأنه يمكن أن يظهر للمشغلين فوائد الصيانة الإنتاجية الشاملة وحل تحدي معروف داخل المؤسسة.
2. استعادة المعدات إلى أفضل حالة تشغيلية
قم بالتخلص من أي معدات غير ضرورية في مكان العمل.
يمكنك القيام بذلك من خلال إتمام الإجراءات التالية:
- التصنيف: التخلص من أي شيء في منطقة العمل غير الضروري.
- ترتيب: تنظيم العناصر المتبقية بعد التخلص من المعدات غير الضرورية.
- تلميع: تنظيف وفحص منطقة العمل للتأكد من أن كل شيء في حالة مثالية.
- توحيد القياسات: إنشاء معايير لإتمام الخطوات الثلاث الأولى.
- المحافظة: التأكد من أن أعضاء الفريق يطبقون دائمًا المعايير التي أنشأتها.
3. البدء في قياس كفاءة المعدات الشاملة
من المهم قياس كفاءة معداتك لأن ذلك يمكن أن يمنحك رؤية حول الإنتاج الإجمالي الذي تخلقه نظام كامل من المعدات.
يمكن أن يساعدك هذا في تحديد مناطق الهدف الجديدة وإنشاء إجراءات ومعايير لكل منها، مما يؤدي إلى نهج شامل لتنفيذ الصيانة الإنتاجية الشاملة.
بالإضافة إلى مساعدتك في تحديد التحديات، يمكن أيضًا أن يساعدك هذا الخطوة في اكتساب المعرفة حول العمليات التي تعمل بالفعل بشكل جيد ولا تحتاج إلى تحسين.
4. التعامل مع التحدي الرئيسي الذي تواجهه العملية الانتاجية
تعامل مع المعدات والعمليات التي تعرض أكبر التحديات أو تسبب أعلى الخسائر للمؤسسة.
يعتبر ذلك مفيدًا لأنه يمكن أن يعزز الإنتاج بسرعة ويوفر رؤى جديدة لكفاءة المعدات الشاملة عند تغيير العمليات المحددة. يمكنك استخدام هذه الخطوة لمتابعة الأسباب الجذرية للتحديات ومعالجتها بسرعة قبل أن تتحول إلى فشل ضمن النظام.
5. إدخال تقنيات الصيانة التنبؤية
أخيرًا، قم بدمج تقنيات الصيانة الإنتاجية الشاملة في الإجراءات التي يمكن للفرق والأفراد القيام بها.
هناك بعض الجوانب لهذه العملية:
- تحديد المرشحين للصيانة التنبؤية: يتمثل ذلك في إبلاغ أعضاء الفريق والأفراد بالمكونات المعرضة للتحديات مثل التآكل والفشل ونقاط الضغط في المعدات.
- تحديد فترات الصيانة التنبؤية: يتمثل ذلك في وضع جدول زمني لمتى يلاحظ المشغلون ويقومون بإصلاح معداتهم، متوازنًا بين وقت التوقف وأهداف الإنتاج.
- إنشاء نظام ردود فعل للتحسين: يتمثل ذلك في مراقبة فترات الصيانة لضمان الحصول على أقصى كمية من وقت الإنتاج والحد الأدنى من وقت التوقف.